Vertical Walls with Concrete Facing Panels
2020
ANTWERP - FLANDERS - Belgium
Jan de Nul - Herbosch Kiere
BRUG VAN DEN AZIJN
Problem
De Vlaamse Waterweg (Flemish Waterway Authority) invested more than 15 million Euro in the construction of the new Burgemeester Eduard Waghemansbrug, better known as Brug van den Azijn. 12.5 million were dedicated to the bridge construction while 2.5 million for the widening of the N130 between the district of Merksem and Deurne. The project included bus lanes in both directions, a one-way cycle lane, and a pedestrian path. The abutments were designed to support a 123 m span arch bridge, approximately 16 m wide. The new bridge clearance was targeted to be 9.1 m high, allowing the passage of ships with four layers of containers. The architects of the project designed an articulated façade for the bridge structures. Therefore, the reinforced soil walls and the true abutments were designed with a 75° inclination.
Solution
Two 300 m long reinforced soil ramps up to 10.5 m high were designed by Maccaferri. The system chosen is called MacRes and it is comprised of concrete panels and ParaWeb polymeric strips. These strips are made of high tenacity polyester yarn encased in a polyethylene (LLDPE) sheath. The reinforcements are the key structural component of the MSE wall system and are mechanically connected to the facing panels through a specially designed connection. According to the design, walls and true abutments were designed with a 75° inclination. The top panels of the reinforced structure had to perfectly match the wall elevation: each top panel was specifically designed to meet the project geometry. The client requested 0.75 m high panels, therefore a horizontal fake joint was included in the panels casting mold. The precise alignment of the panel joints was possible thanks to AutoCad modeling based upon precise topographic measurements. No corner elements were cast for this project. Panels were properly aligned to create a continuous wall facing. Cladding elements were manufactured to cover the concrete abutments and provide the same aesthetical finishing adopted for the wall structures.
Used Products
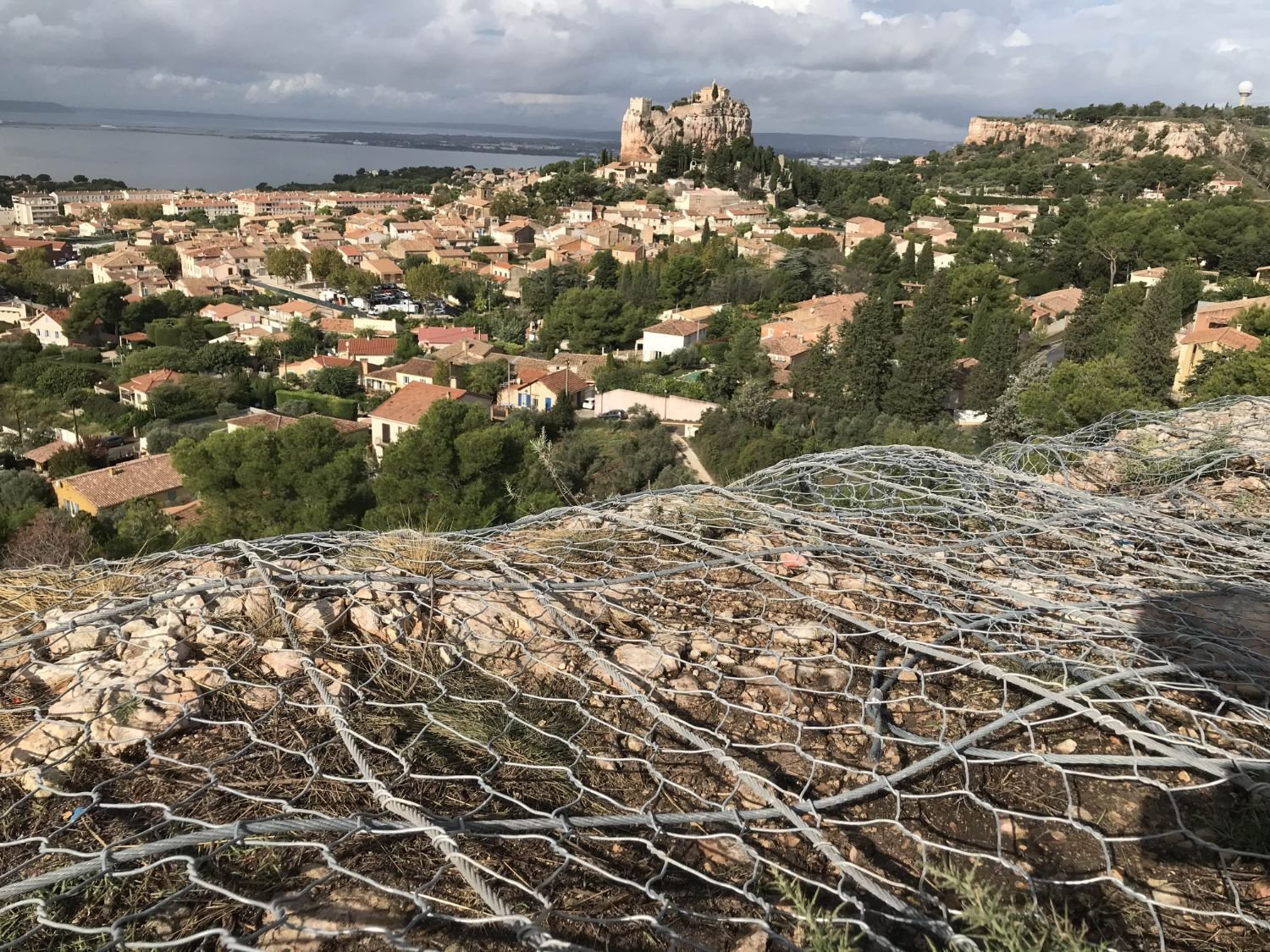